Precise Imprecision
Flexible Construction with Robotic Fabric FormworkPrecise Imprecision from Yi-Liang Ko on Vimeo.
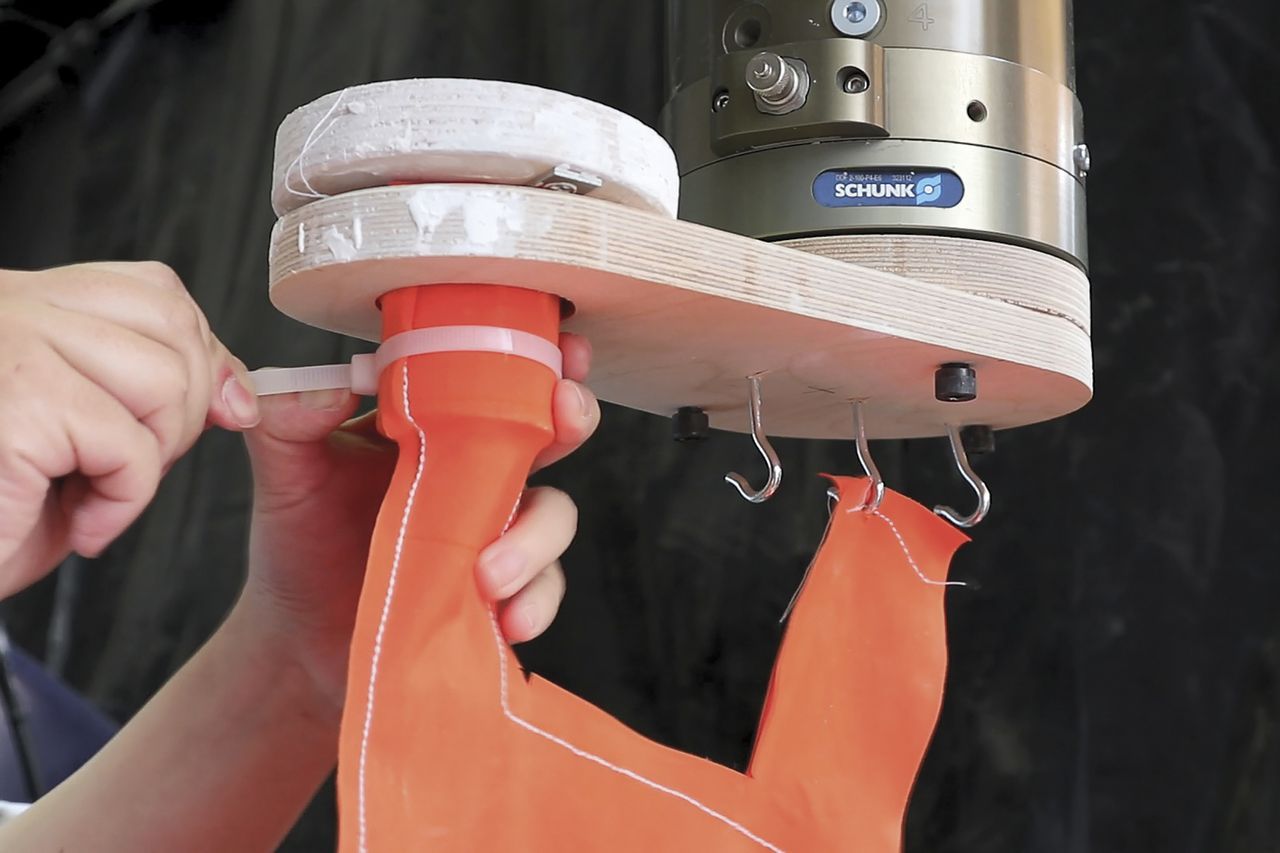
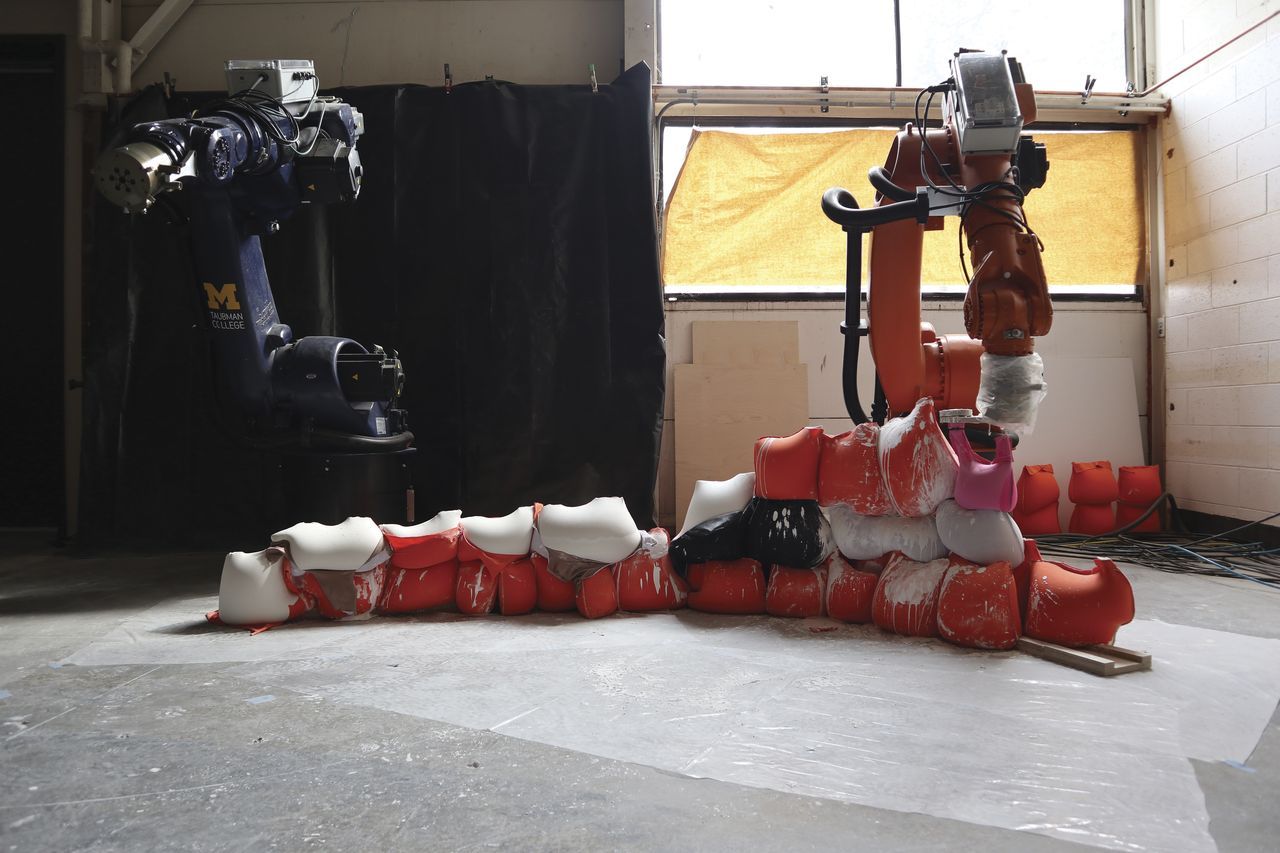
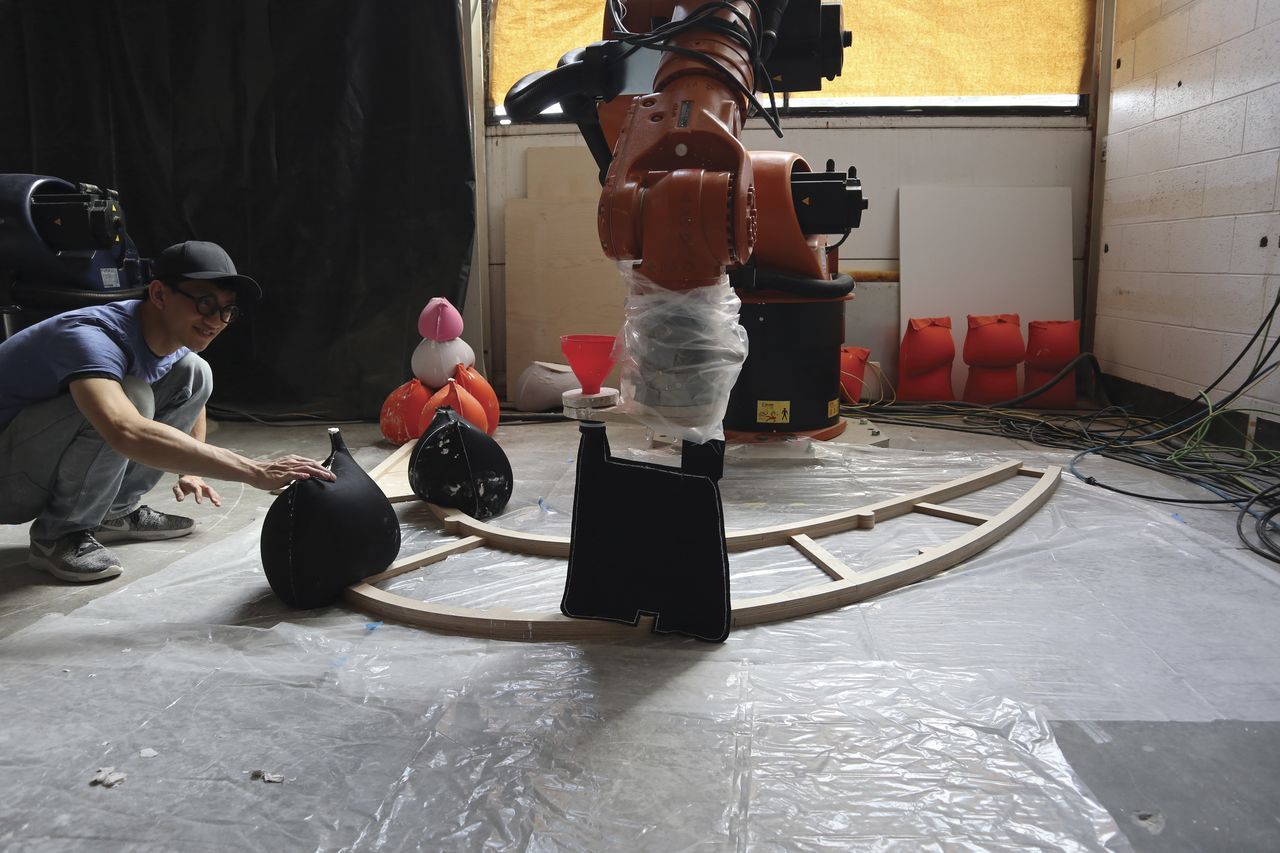

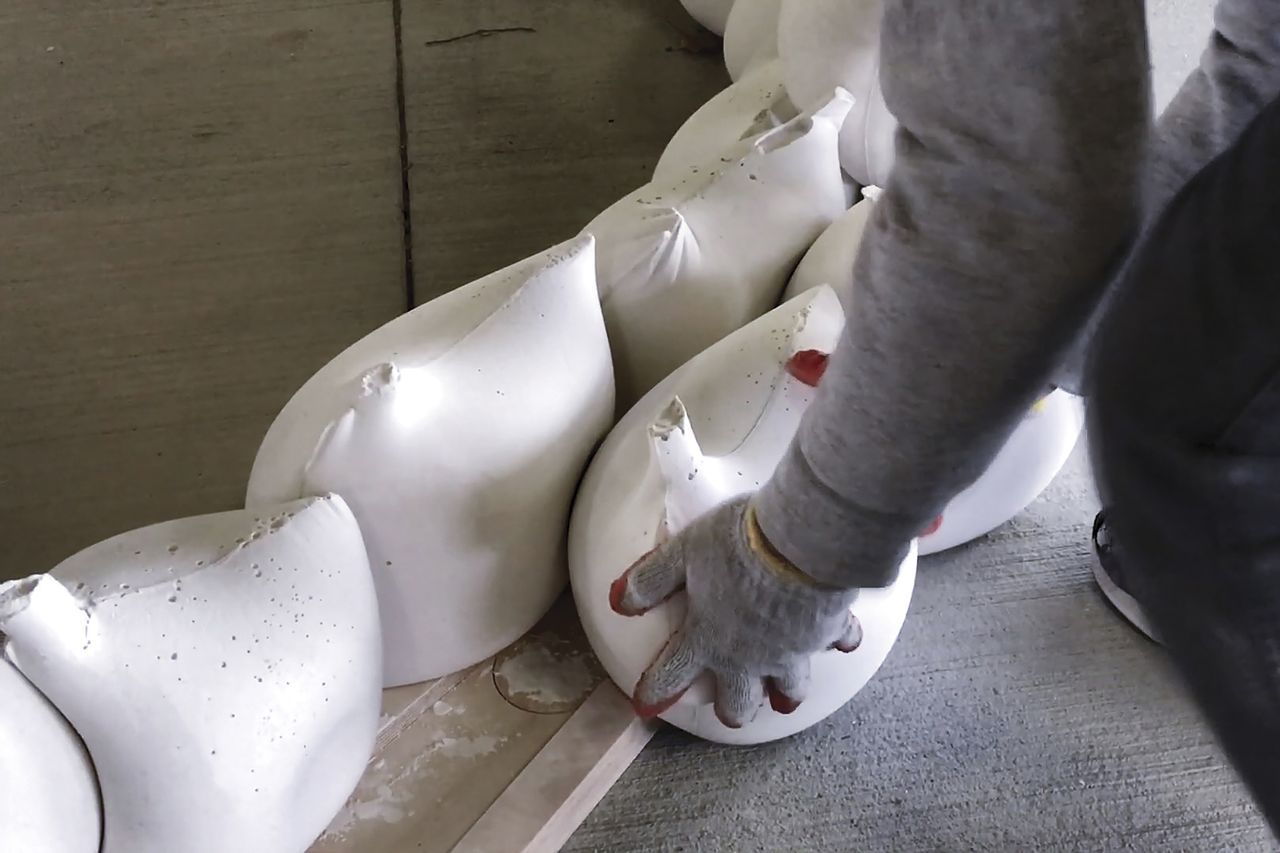
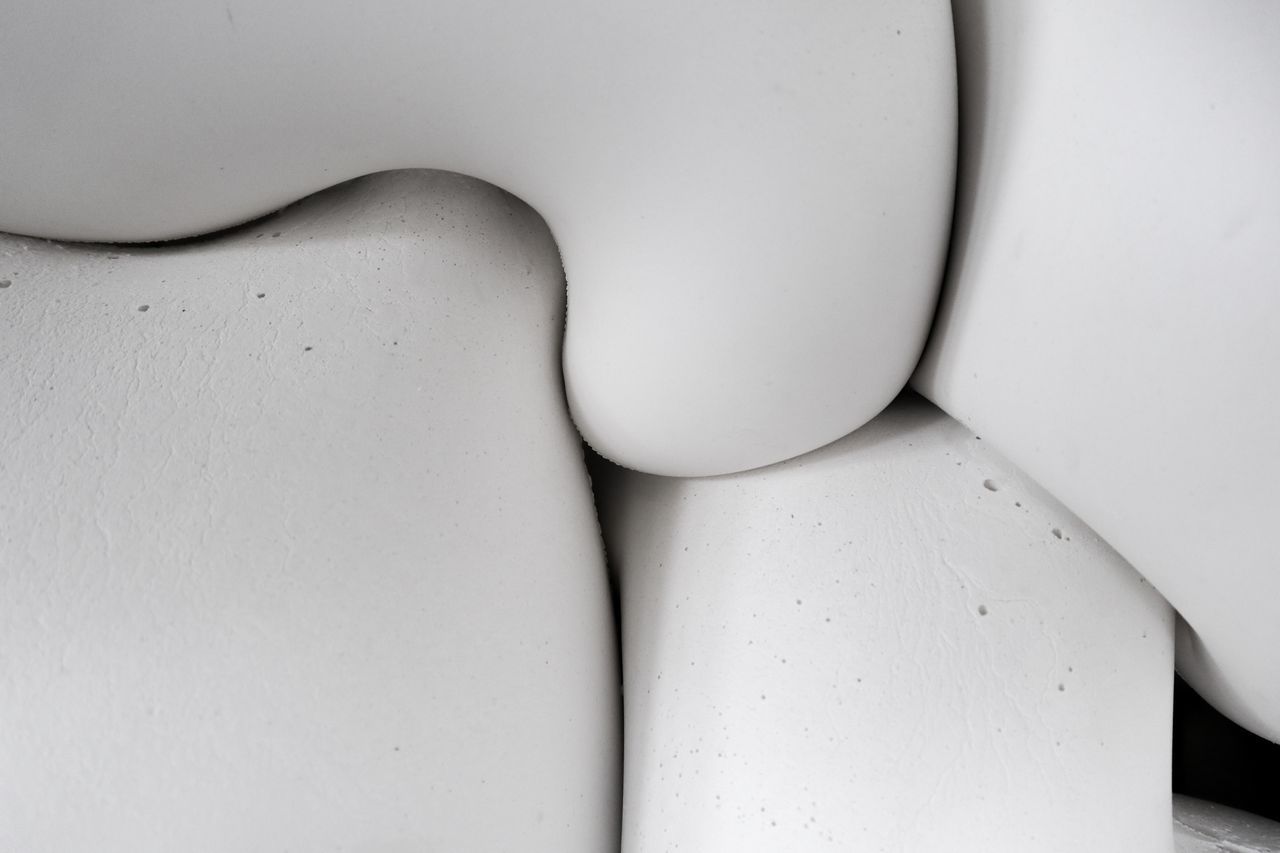



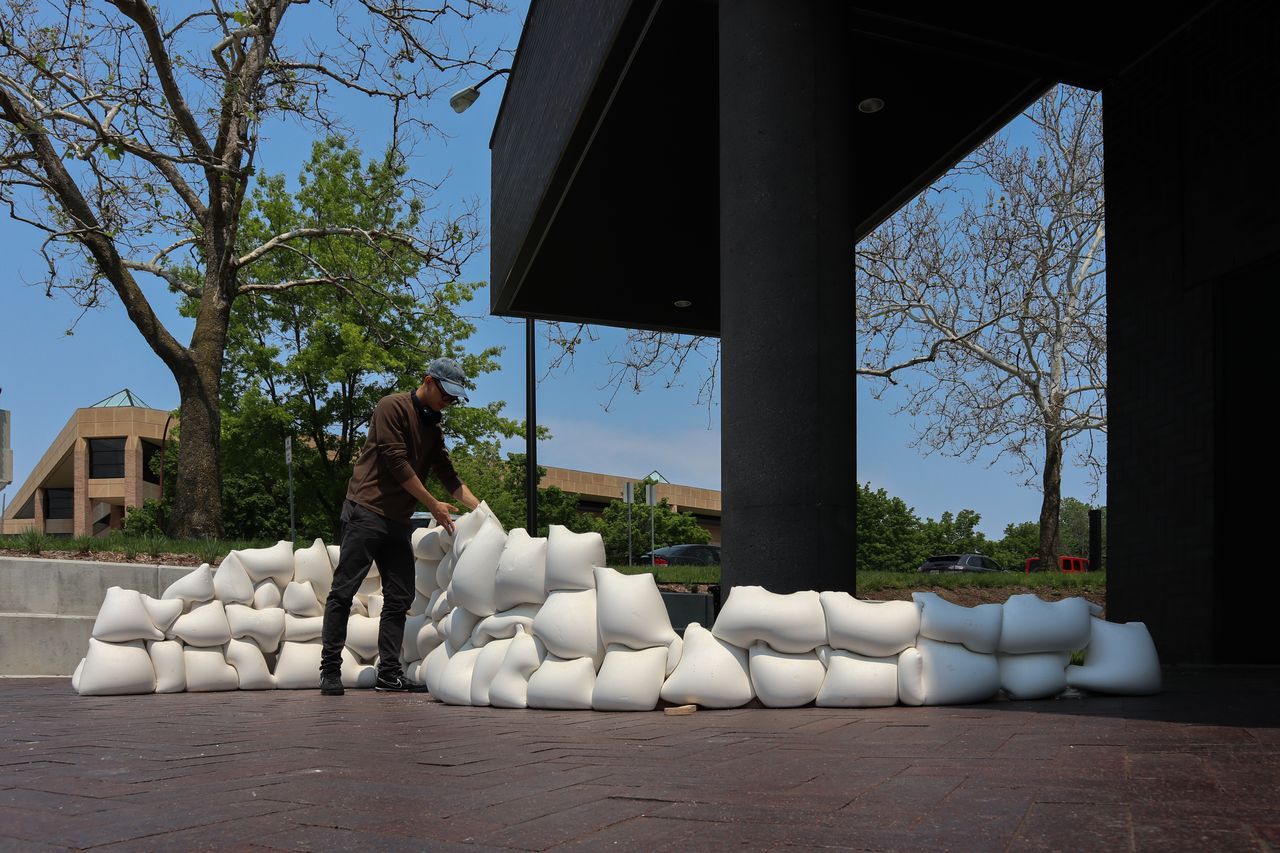
Flexible
Formwork
On September 8, 1897, Gustav Lilienthal hung
sufficiently impermeable fabric in the catenary form between the beams to build
a fireproof ceiling. This invention created the first customized natural
geometry during the fabrication in situ. (The Fabric Formwork Book, 2017)
Flexible formwork has a difficult implementation in regular constructions, but
it expands the vision of formwork via creating complex formation in statistics.
For instance, in recent works by Andrew Kudless (Bodies in Formation, 2011) and
Form Found Design (Mars Pavilion, 2017), flexible formwork integrates into
advanced technologies among various applications. Combining thoughts of
collaborating robotic assembly and the textile forming in the plaster cast on
site from precedents, Precise Imprecision demonstrates a new methodology –
robotic stack casting.
Methodology
The technique combines dynamic performance and
computational configuration to create natural shapes in digital practice.
Materially, flexible form-fit presents customized form from precast units
environment. Parametrically, robotic assembly produces controlled data and
diminishes labor-intensive manufacturing. Robotic stack casting integrates cast
and construction practices simultaneously to bring out unique aesthetics and
identity boundaries. The elastic form-fit pattern relates to the notions of
dry-fitted Inca masonry. Compared with the measurement and carving in their
ancient artifact, this flexible construction procedure accelerates the form-fit
manner.
Computation and Morph Grammars
As an experiment, a full-scale prototype
converges the similarity, transition, and contrast between the physical and
digital worlds to evolve its private aggregation and numerical parameters.
Based on recent work by Brandon Clifford and Wes McGee on digital Inca masonry
(Cyclopean Cannibalism, 2017), different shape, volume, and order outline three
roles as Base, Fill and Keystone in the fabrication. For stimulating the dual
wythe of curvature to Inca masonry, the Base, Fill and Through stones are
re-defined to cooperate with robotic construction and initial assembly. Fabric
formwork is a combination of internal and external pressures. Converting the
solid masonry into soft behavior, physical parameters between size, geometry,
overlap, and arrangement influence both global and local systems. In order to
digitize robotic stack casting, assembly rules and parameters generate a unique
moment for drawing code which merges the deformation into the dramatic mass
pattern.
Fabrication
In the final studies, 116 units are shaped and
aggregated in an efficient workflow by two KUKA robots with the customized end
effector. As a versatile technique on site, the curved wall is split into two
sections to increase the overall dimension; the base track which aims to locate
stones in the first layer stabilizes the structure and extends the purpose of
the form-fit seat; the collaboration within robots investigates the potential
of automatic adjustable construction without formwork. The prototype displays
the weakness of casting efficiency from robotic manufacturing and the
impossibility of concrete in stack casting, but it sets a game beyond the gap
between “precision” and “imprecision” in both analog and digital processes.
Precision and Imprecision
year: Winter 2019
type: Digital Fabrication / Material Research course: MS Capstone, Taubman College
partner: Hong-Fen Lo
advisor: Glenn Wilcox
status: Completed
size: 80” X 80” X 40”
location: Ann Arbor, MI
On September 8, 1897, Gustav Lilienthal hung
sufficiently impermeable fabric in the catenary form between the beams to build
a fireproof ceiling. This invention created the first customized natural
geometry during the fabrication in situ. (The Fabric Formwork Book, 2017)
Flexible formwork has a difficult implementation in regular constructions, but
it expands the vision of formwork via creating complex formation in statistics.
For instance, in recent works by Andrew Kudless (Bodies in Formation, 2011) and
Form Found Design (Mars Pavilion, 2017), flexible formwork integrates into
advanced technologies among various applications. Combining thoughts of
collaborating robotic assembly and the textile forming in the plaster cast on
site from precedents, Precise Imprecision demonstrates a new methodology –
robotic stack casting.
Methodology
The technique combines dynamic performance and
computational configuration to create natural shapes in digital practice.
Materially, flexible form-fit presents customized form from precast units
environment. Parametrically, robotic assembly produces controlled data and
diminishes labor-intensive manufacturing. Robotic stack casting integrates cast
and construction practices simultaneously to bring out unique aesthetics and
identity boundaries. The elastic form-fit pattern relates to the notions of
dry-fitted Inca masonry. Compared with the measurement and carving in their
ancient artifact, this flexible construction procedure accelerates the form-fit
manner.
Computation and Morph Grammars
As an experiment, a full-scale prototype
converges the similarity, transition, and contrast between the physical and
digital worlds to evolve its private aggregation and numerical parameters.
Based on recent work by Brandon Clifford and Wes McGee on digital Inca masonry
(Cyclopean Cannibalism, 2017), different shape, volume, and order outline three
roles as Base, Fill and Keystone in the fabrication. For stimulating the dual
wythe of curvature to Inca masonry, the Base, Fill and Through stones are
re-defined to cooperate with robotic construction and initial assembly. Fabric
formwork is a combination of internal and external pressures. Converting the
solid masonry into soft behavior, physical parameters between size, geometry,
overlap, and arrangement influence both global and local systems. In order to
digitize robotic stack casting, assembly rules and parameters generate a unique
moment for drawing code which merges the deformation into the dramatic mass
pattern.
Fabrication
In the final studies, 116 units are shaped and
aggregated in an efficient workflow by two KUKA robots with the customized end
effector. As a versatile technique on site, the curved wall is split into two
sections to increase the overall dimension; the base track which aims to locate
stones in the first layer stabilizes the structure and extends the purpose of
the form-fit seat; the collaboration within robots investigates the potential
of automatic adjustable construction without formwork. The prototype displays
the weakness of casting efficiency from robotic manufacturing and the
impossibility of concrete in stack casting, but it sets a game beyond the gap
between “precision” and “imprecision” in both analog and digital processes.
Precision and Imprecision
The definition of accuracy bounces within the collaboration of robots and fabrics. Precise robotic assembly causes inexact placement; imprecise fabric deformation creates accurate connections. The chaotic pattern implies digital methodology and finds its position with little effort. Precise Imprecision raises the phenomenon of providing tolerance itself and breaks the stereotype that precise manufacturing and robotic fabrication are inseparable. The research outlines the potential of combining with generative coding and sensor feedback to establish an interactive, automatic building method. This autonomous behavior designs and constructs simultaneously through the process of data accumulation and revision.
year: Winter 2019
type: Digital Fabrication / Material Research course: MS Capstone, Taubman College
partner: Hong-Fen Lo
advisor: Glenn Wilcox
status: Completed
size: 80” X 80” X 40”
location: Ann Arbor, MI